Air Compressor Motors 101: Types, Power Ratings & Best Uses
- limaindustial
- Jul 10
- 6 min read
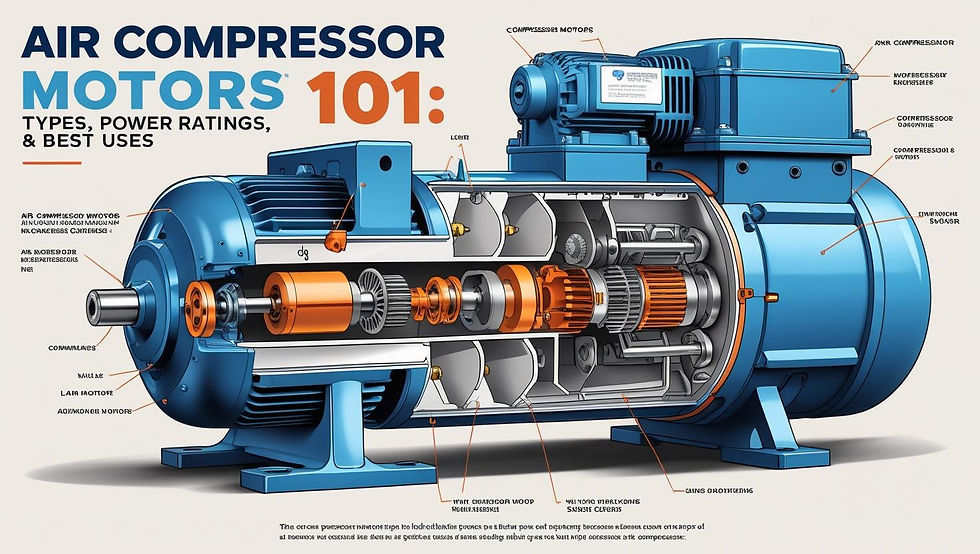
In any industrial or commercial setting, compressed air systems serve as a backbone for numerous operations—from powering pneumatic tools to managing material conveyance and assembly line automation. At the heart of every air compressor system lies the motor, which provides the necessary power to drive the entire compression process.
Selecting the correct motor isn’t just about ensuring functionality—it’s about optimizing performance, extending equipment lifespan, reducing energy costs, and ensuring uninterrupted operations.
Yet with so many motor types, configurations, ratings, and enclosures to choose from, decision-makers often face confusion. This detailed guide will help you understand the key aspects of air compressor motors, allowing you to choose the right one for your application.
What Is an Air Compressor Motor?
An air compressor motor is an electric or combustion-powered device that converts electrical or fuel energy into mechanical motion to compress air. Most industrial air compressor systems rely on electric motors due to their efficiency, lower operating cost, and cleaner operation.
These motors can be either directly mounted on the compressor or connected via belts and pulleys. Regardless of configuration, the motor's torque and speed characteristics determine how quickly and efficiently the compressor can deliver air pressure and flow (CFM) to tools or processes.
Air Compressor Motor Types Explained
The right motor type depends on usage, power availability, environment, and required output. Here are the most common air compressor motor types:
Single-Phase Motors
Common in residential or light-duty setups, single-phase motors are easy to install but have limited power capacity, usually below 5 HP. They operate on standard 220V circuits and are ideal for small shops or garages.
Three-Phase Motors
Designed for industrial applications, three-phase motors offer superior efficiency and smoother operation. They deliver more power, ranging from 5 HP to hundreds of HP, and handle continuous or heavy-duty cycles with ease.
Open Drip-Proof (ODP) Motors
These motors have an open housing that allows air to flow freely over internal components. While cost-effective and sufficient for clean environments, they are vulnerable to dust and moisture.
Totally Enclosed Fan-Cooled (TEFC) Motors
TEFC motors are sealed against contaminants and use an external fan to dissipate heat. These motors are ideal for industrial plants, dusty warehouses, or outdoor environments where debris and weather can compromise performance.
Explosion-Proof Motors
Used in hazardous environments where flammable gases or dusts may be present, explosion-proof motors prevent any internal spark or heat from escaping the housing. These are mandatory in oil, gas, chemical, and food-grade facilities.
High-Efficiency Motors (IE3/IE4)
These motors are engineered to consume less energy while delivering the same or better performance. They are ideal for operations running multiple compressors or high-hour usage applications.
VFD-Compatible Motors
Motors designed to be paired with Variable Frequency Drives (VFDs) allow for speed control and soft-start capability. This results in smoother operation, less wear on components, and energy savings through load-based operation.
Power Ratings and Horsepower Ranges
Air compressor motors are available in a wide range of horsepower (HP) ratings to suit different needs. The motor’s HP determines the amount of air (CFM) and pressure (PSI) the compressor can deliver. A 5 HP motor might suffice for a small workshop, while a 150 HP motor is more appropriate for a manufacturing plant.
Key considerations include:
Duty cycle: Whether the motor runs continuously or intermittently.
Peak vs. continuous load: Ensure the motor’s rating matches the compressor’s load curve.
Safety factor: Always select a slightly higher HP to accommodate startup surges and extra demands.
Voltage, Frequency & Frame Size Considerations
Choosing the correct electrical specs is critical for compatibility and safe operation.
Voltage
Most industrial motors operate on 220V, 380V, 440V, or 660V, depending on your region and facility wiring. Higher voltage motors are often more efficient and reduce amperage, minimizing heat buildup and wiring costs.
Frequency
Motors typically run on either 50Hz or 60Hz. Running a 60Hz motor on a 50Hz supply (or vice versa) without proper adjustment will result in speed mismatches and performance issues.
Frame Size
The motor frame defines the physical dimensions, mounting hole pattern, and shaft height. Proper frame matching ensures seamless installation with your compressor base.
Insulation Class
Higher insulation classes (Class F, H) allow motors to tolerate higher temperatures without degrading performance.
Selecting the Right Motor for Your Compressor
Before purchasing, use this practical checklist:
Determine Load Type: Is your compressor single-stage or two-stage? Does it require consistent high pressure or fluctuating air flow?
Calculate Duty Cycle: Will it run 8 hours a day or continuously? This impacts motor size and cooling requirements.
Review Ambient Conditions: Dust, humidity, temperature, and altitude influence enclosure type.
Match Voltage and Frequency: Ensure compatibility with your facility’s electrical supply.
Plan for Maintenance: Choose a motor type that is easy to service or replace based on your in-house capabilities.
Industrial Use Cases for Different Motor Types
Each industry has specific demands. Here’s a quick overview:
Manufacturing Plants: Heavy-duty three-phase TEFC or VFD-compatible motors to handle 24/7 operations.
Automotive Garages: 5–15 HP motors, often in TEFC or ODP configuration.
Food Processing Facilities: Explosion-proof and washdown-rated motors to meet hygiene and safety standards.
Mining and Construction: Rugged, dust-resistant motors with high torque and cast-iron housings.
Energy Sector: High-efficiency motors designed to handle fluctuating loads and strict safety standards.
Common Air Compressor Motor Problems (and How to Avoid Them)
Understanding failure points helps prevent downtime. Common issues include:
Overheating: Caused by blocked airflow, under-sized motors, or poor insulation.
Voltage Drops: Inconsistent voltage supply can damage windings and reduce performance.
Bearing Failures: Lack of lubrication or misalignment increases friction and wear.
Ingress of Contaminants: Dust and moisture can enter open motors, damaging internal components.
Improper Start/Stop Cycles: Frequent cycling stresses the motor—this is where VFDs help.
Preventive Maintenance & Best Practices
Routine maintenance prolongs motor life and ensures consistent performance.
Inspect Bearings Regularly: Listen for abnormal noise or vibration.
Clean Vents and Housing: Remove dust buildup that can trap heat.
Lubricate as Per Schedule: Avoid over- or under-greasing.
Monitor Vibration: Misalignment and imbalance can cause premature failure.
Test Insulation: Check insulation resistance to ensure electrical integrity.
Cost and Energy Efficiency Breakdown
Motor Type | Initial Cost | Energy Efficiency | Maintenance | Best Use Case |
Single-Phase | Low | Moderate | Easy | Small shops, garages |
Three-Phase | Medium | Good | Moderate | Manufacturing, heavy-duty applications |
VFD-Ready | High | Excellent | Low | Dynamic load environments |
High-Efficiency (IE3/4) | High | Exceptional | Low | Continuous operations, energy-saving |
When to Upgrade or Replace Your Motor
It may be time to upgrade if:
Your motor frequently trips or overheats.
It fails to maintain stable pressure under load.
Spare parts are hard to source or obsolete.
You're paying more in energy bills despite stable usage.
You’re expanding operations and need more power or features.
A new motor can increase productivity, reduce maintenance, and enhance energy efficiency.
Why Choose Lema Industrial Air Compressor Motors
At Lema Industrial, we understand that every business has unique operational demands. That’s why we offer a diverse range of air compressor motors engineered for durability, reliability, and high efficiency. Our motors are built with precision engineering and tested for extreme conditions—whether you're operating in a factory, a food-grade facility, or an outdoor construction site.
With customizable voltage, enclosure, and horsepower options, our motors provide maximum flexibility. Each unit is backed by quality assurance protocols and supported by our experienced technical team to ensure a smooth experience from installation to operation.
Conclusion
Choosing the right motor for your air compressor system isn't just about power—it's about making a strategic investment in performance, reliability, and cost efficiency. From voltage requirements to environmental conditions and usage cycles, many variables influence which motor is best for your application.
By understanding your operational needs and the features of various motor types, you can confidently make a selection that aligns with your goals and ensures consistent productivity. For this, you should visit this air compressor motor manufacturer and get the desired motor based on your usage.
FAQs
What size motor do I need for a 10 HP air compressor?
You typically need a 10 HP rated motor with matching voltage, frequency, and duty cycle specs to ensure safe and optimal operation.
Can I use a VFD with any air compressor motor?
No. Only VFD-compatible motors with appropriate insulation and bearings should be used with variable frequency drives.
What's the difference between ODP and TEFC motors?
ODP motors are open and better for clean environments, while TEFC motors are sealed to prevent dust and moisture intrusion.
How often should I service an air compressor motor?
Basic checks should be done monthly, with full maintenance every 3–6 months, depending on usage intensity.
Is it worth upgrading to a high-efficiency IE4 motor?
Yes, especially for continuous-duty systems. While upfront costs are higher, the energy savings and reduced heat generation justify the investment.
Comments